The Descendants of the Divine Architect
The shilpis or stonemasons who claim to be descended from the divine architect of the universe, Visvakarma, were one of the five most respected and leading artisan guilds under the Pandya, Chola, Pallava, and other dynasties who ruled South India, especially the areas of Tamil Nadu. Although the buzz around the craft has declined in the present times, this lineage of stonemasons continues to work with ancient methods of chipping, handling, and extracting the local granite reserves.
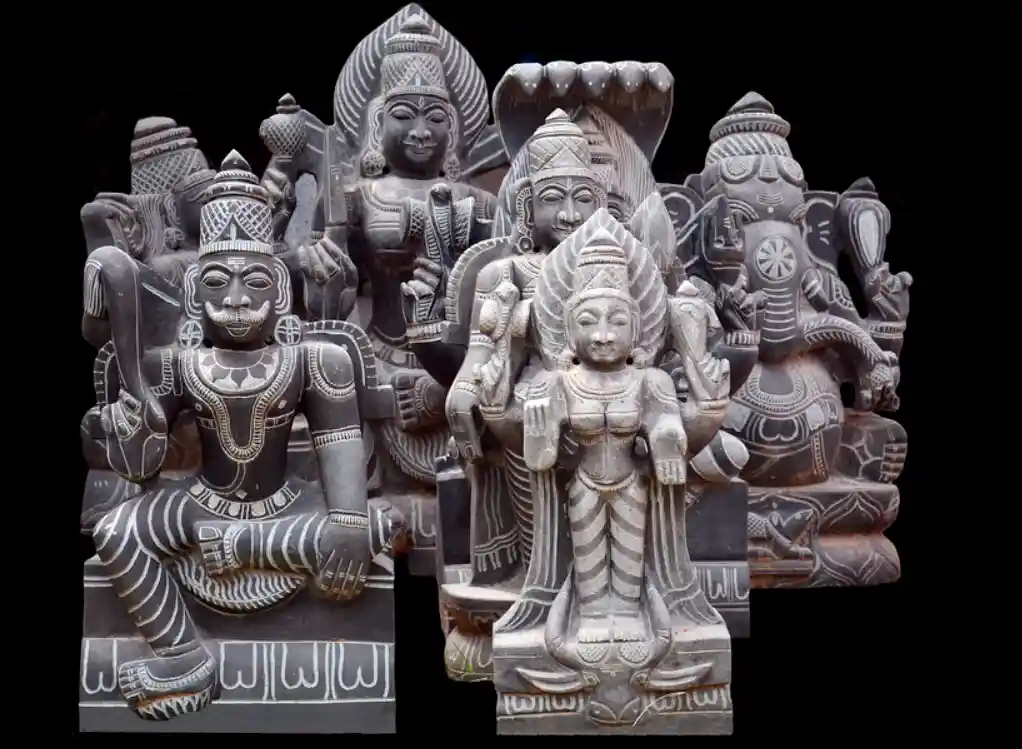
The exquisite work of the stonemasons. Source: Flickr | Manfred Sommer
The temple town of Madurai and the monuments of Mahabalipuram are some of the most sought-after tourist locations, visited by flocks of people eager to experience the sheer beauty of South India’s cultural wealth. The artisans who sculpted and built these temples hundreds of years ago managed to capture in stone the enchanting visualizations of myths and the events of Tamil Nadu’s past.
Medieval Tamil society was largely agrarian,$^1$ and work was centered around the locality, i.e., the temple, palace, land tenures, and day-to-day activities. Naturally, the artisan communities were highly respected and formed a major part of society. Five of these occupational groups—tattan (goldsmiths), kannar (brass smiths), karuman/kollan (blacksmiths), tachchan (carpenters), and shilpi/kaitachchan (masons)—came to be known as *kammalars (*smiths). In Kadamba, Rashtrakuta, and Ganga inscriptions, they are referred to as Viswakarma or Viswakarmacharyas$^2$, paying homage to their alleged descent from the divine architect of the gods, Visvakarma.
Burton Stein, the author of Peasant, State and Society in Medieval South India, speculates that kammalas were the offspring of kshatriya fathers and vaishya mothers, who also wore yajnopavita, the sacred thread$^3$. These artisan guilds, who were engaged in work ranging from the sculpting of the temple gopurams to making chariots and carts used by the locals, were patronized by the kings. Even the village assemblies were willing to allocate tax-free lands called taccakani, tattarakkani, acaiyakkani, and so on to them.
The name kammalar or kannalan translates to “the one who rules the eye” since the articles they crafted were believed to have opened the eyes of the commoners to beauty. Such was their status in the economy that according to an epigraph$^4$ from Alangudi **dated 1264 AD, kammalas used to raise funds among their members for the construction of village pavilions or temples. Under the rule of Maravarman **Sundarapandya II, the stonemasons who worked on temple construction set aside one-tenth and the architects one-eighth of their income (tachchakkuru) for the mutt.
Today, the masons in regions like Eriyur in Tamil Nadu use ancient techniques of hand-leveling the granite to make stones for grinding masala pastes at home. Eighty-two-year-old artisan and sthapathi, Nataraja Pillai from Nagercoil designs and executes new temple constructions in the region as well as the restoration and rehabilitation of old temples and statues. He had chosen the profession because all his forefathers had been involved in it.
"They've been making stone slabs for generations. But when they see [them], in this kind of composition, they realize that that they can make anything."
— Architect Anupama Kundoo, who designed the BE OPEN's ‘Made In… India Samskara exhibition’ in New Delhi in 2014.
Architect Kundoo worked with the local craftsmen in Eriyur to design an undulating landscape made from hand-leveled granite modules, which was used as a platform to display objects from the exhibition. Even the craftsmen who had toiled on the project for six weeks were surprised at the unconventional use of their expertise.
Going forward, one can only be excited about the prospects of combining contemporary design with the technical skills of South India’s divine craftsmen.
Although the artisans were highly encouraged by the kings and the locals, most of them remained anonymous since the architects and masons did not fuss over engraving their names or faces on temples and inscriptions. Interestingly though, one inscription did carry the names of the sthapathis. With the help of this, Dr G.Balaji from C.P.R. Institute of Indological Research, Chennai, in his paper “Discovering the Sculptor of Mamallapuram,” speculates that the chief architect of the Mahabalipuram monuments during the Pallava rule was also the sculptor whose image is engraved on the extensively sculpted panel called Arjuna’s Penance, located behind the Talasayana Perumal Temple, which is situated at the entrance of Mamallapuram.
The reasons for his speculation are quite intriguing. Scholars like R. Nagaswamy believed that some of the names of the artisans found on small rocks called Nondivirappan Kudiraittoti near Mamallapuram could be of the sthapathis who constructed the monuments. One of them was Kevatapperuntaccan, where “perun taccan” translated to “chief architect.”
On Arjuna’s Penance*,* towards the left side, below the level of an image of Lord Shiva, the panel is unfinished and shows a stone mason sculpting a rock.
The sculpture was detailed enough to show the headdress, a thin ornamental chain, the sacred thread adorned by the Shilpi, and a dagger: **a sign of the authority or talent of the chief architect in ancient Tamil society.
So, the sculptor could have been Kevatapperuntaccan.
The kings from the Pandya, Chola, and Pallava dynasties hired stonemasons to engrave royal orders on stones and copper plates, thereby increasing the demand for the profession to maintain complex government, local, and central records. Stonemasons were then chosen on a hereditary basis and it translated into a family profession.
But how was the work carried out?
Inscriptions at Tiruvarur refer to three different categories of craftsmen who represented the stonemasons: sutragrahi, tasked with measuring and blocking out stones before carving; vartaki, the stone dresser; and shilpi or kaltachchan, the actual sculptor. The sthapathi acted as the vastuthajan who knew architecture.
The journey to creating an ornate pillar or sculpture starts with a process known as aravadittal by Tamil stonemasons even today. To obtain a workable core from the identified boulder, the unwanted rock mass is sectioned off and trimmed by removing large blocks. To do this, they would first make a line of small holes in the stone at short intervals with the help of a chisel and then insert either wooden or flat-edged iron wedges in them. The pressure created by hammering the iron wedges, or the contraction and expansion of the wooden piece when water was poured on it, generated cracks in the stone.
Once a convenient core was chiseled out, carving was done from top to bottom, especially in the case of monolithic structures. This was especially useful for the masons as the uncut rock served as a platform to rest on while carving.
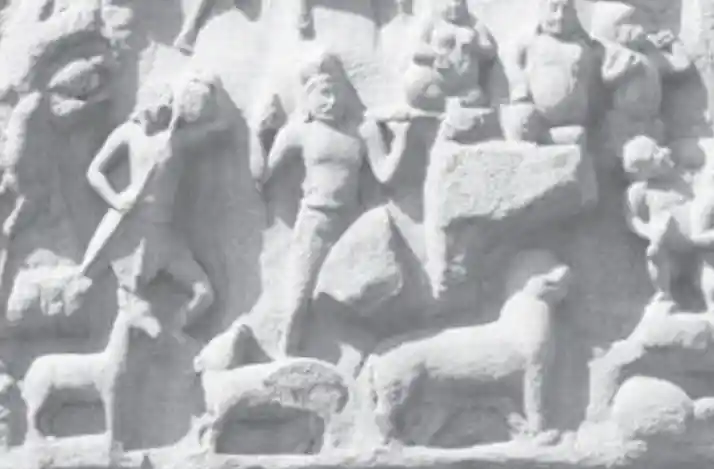
View of the sthapathi in Arjuna’s Penance. Source: Discovering the Sculptor of Mamallapuram | Dr G.Balaji
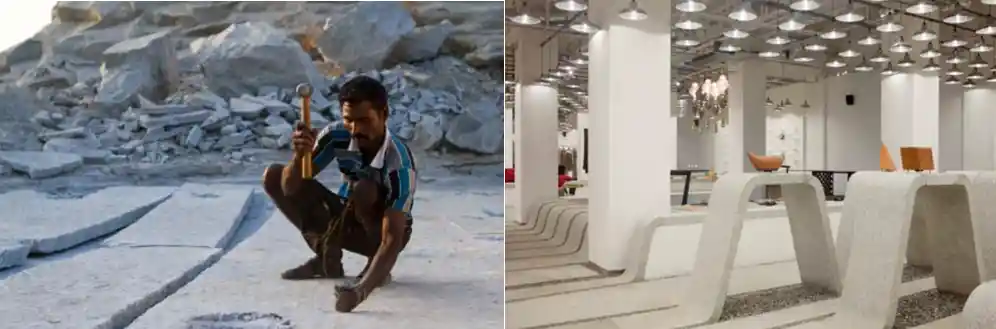
Left: Workers in Eriyur hand-leveling the granite. Right: BE OPEN's ‘Made In… India Samskara exhibition’ designed by Anupama Kundoo. Source: Dezeen
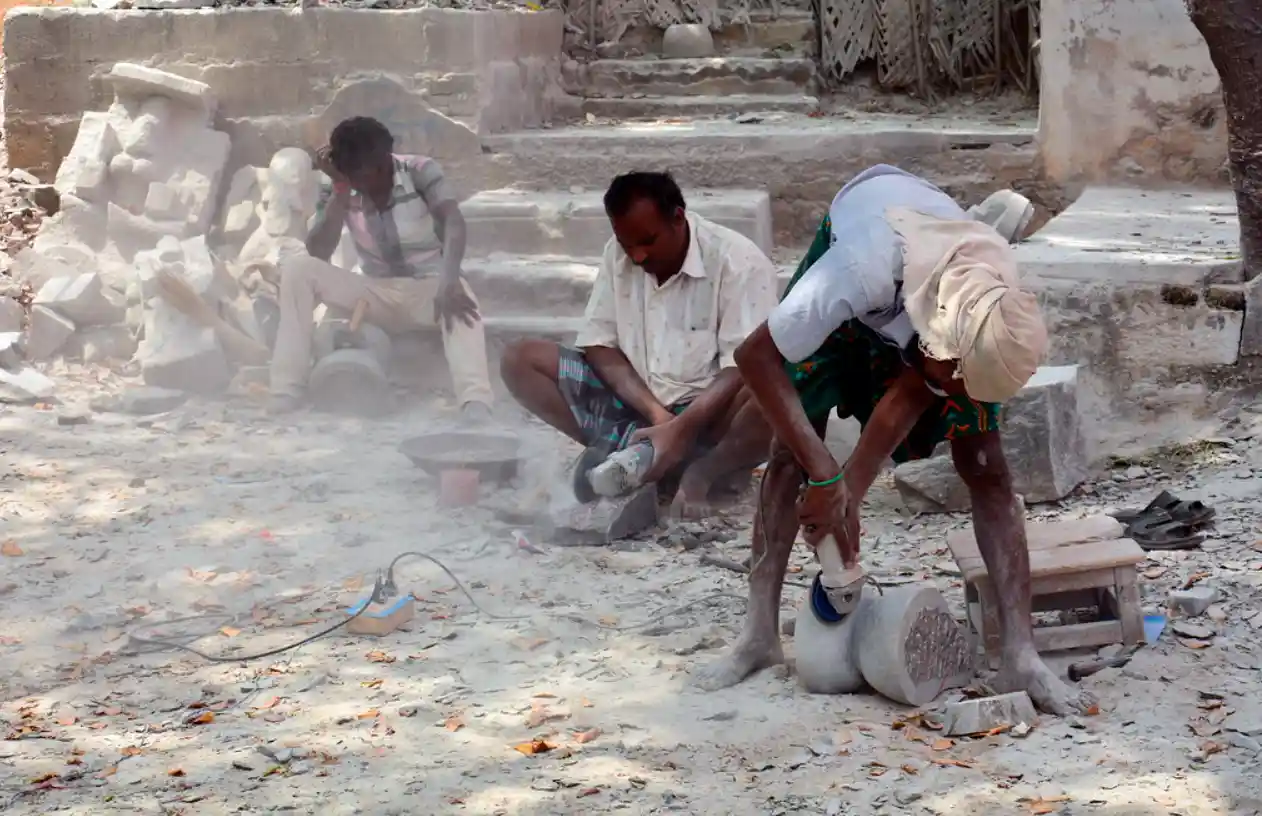
Contemporary masons integrate technology with their skills. Source: Flickr | Manfred Sommer
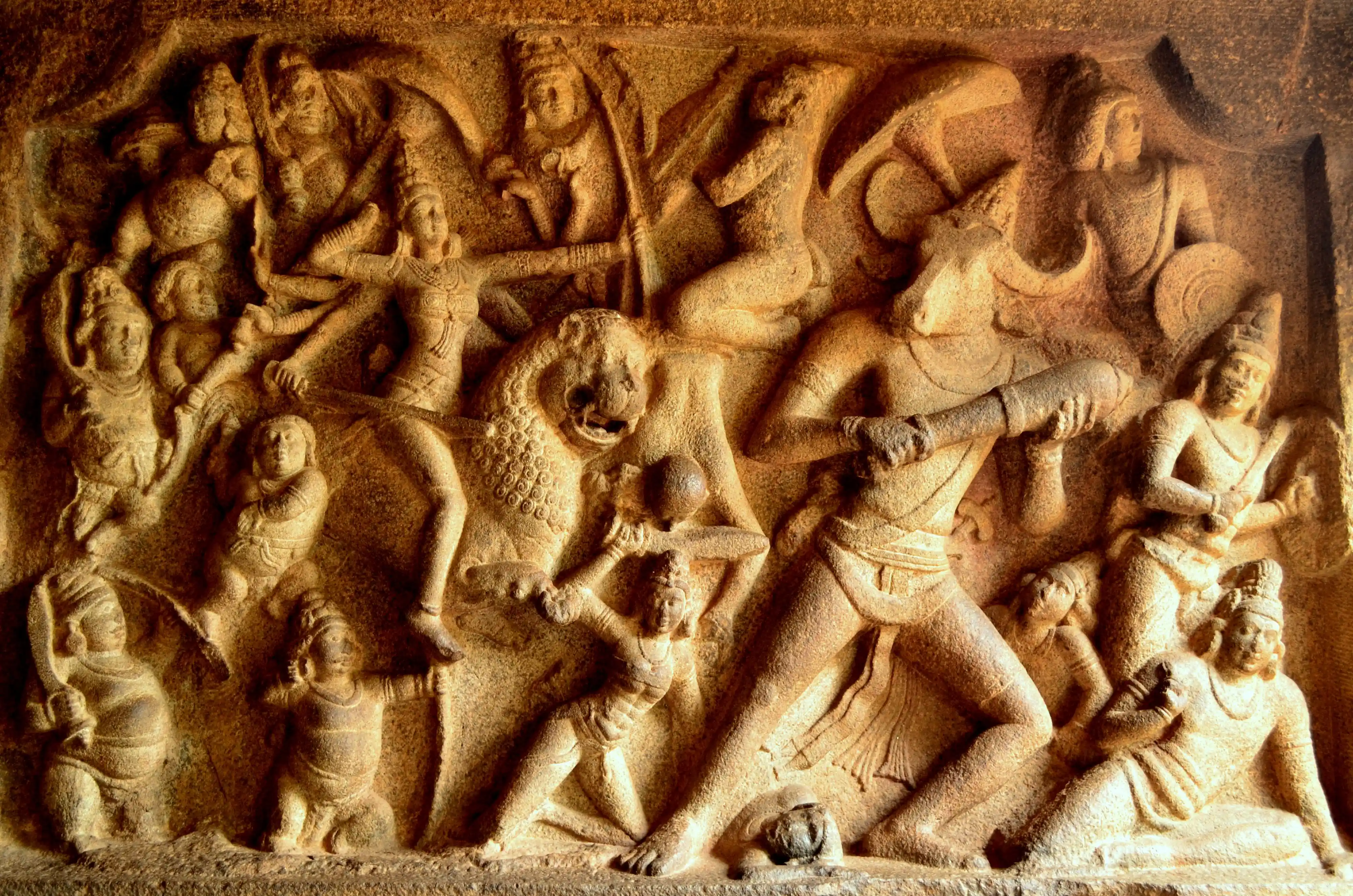
Carved stone panel at Mahabalipuram. Source: Flickr | Sudarsan Gopalan
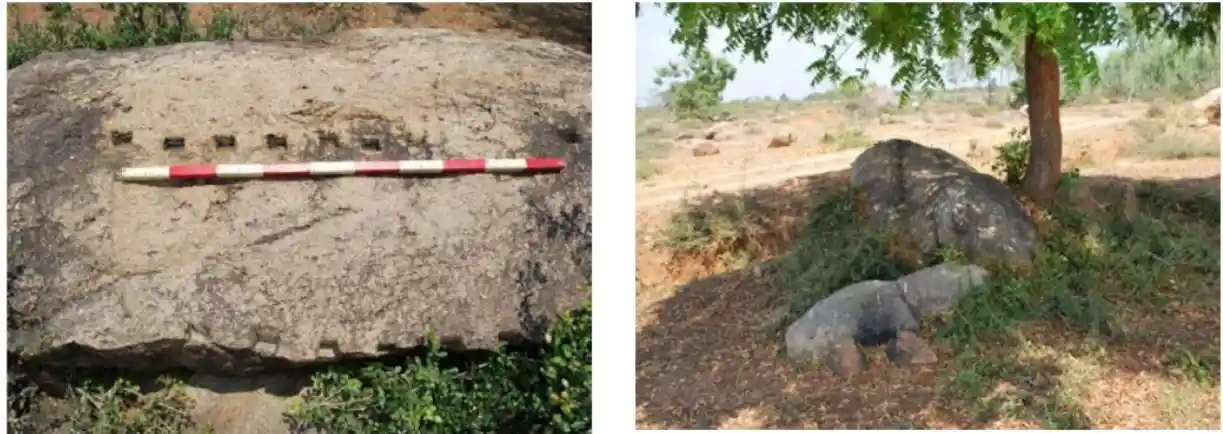
Left: Capstone at Amur with the line of holes created for wedges. Right: Capstone from Siruthavoor with a line of holes for cutting or shaping the stone. Source: Siruthavoor: An Iron Age-Early Historical Burial Site, Tamil Nadu, South India by Smriti Haricharan

Nataraja Pillai working on statues. Source: Thannal| Ramani Rajam